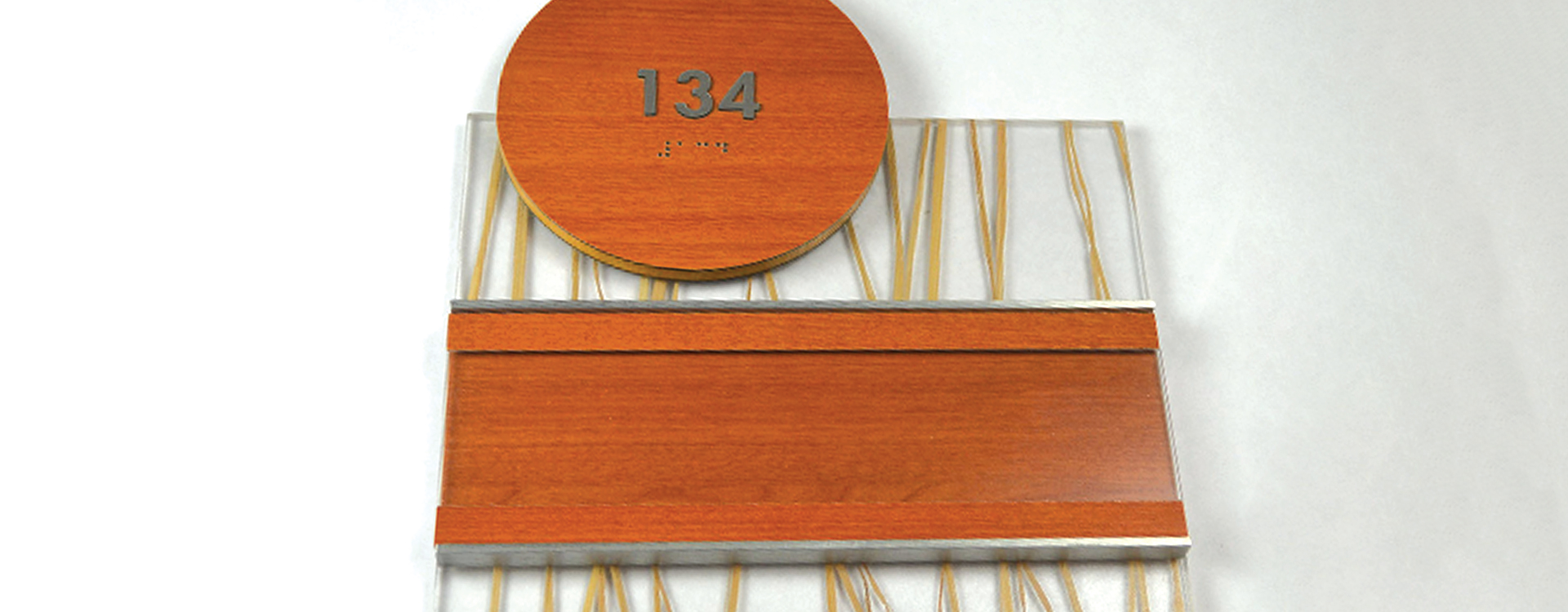
Many signage professionals have a method to stick in their ways of manufacturing signage. It’s easy to look at common methods of signage, ADA signage specifically, and think there’s no need to change something that isn’t broken. While the various methods of creating ADA signage like photopolymer are efficient, the expert team at Viscom Wholesale Signage seeks to revolutionize their production methods. By staying at the front of technological trends, our team provides the highest quality, most cost-effective signage with efficient mobilization.
Our team has recently taken on the capabilities of UV printing, or PrintPolymer, as we like to call it. The printing process is immediate with a digital upload, requires no creation of film or templates, and creates one single ready-to-ship product. Our printers make us the most capable ADA fabricators in the country, with speedy printing production, enhanced ability to create textures and designs, printing multiple layers, front printing, and back printing. The efficiency of PrintPolymer beats out photopolymer and other methods, being able to work on more signs at a faster rate.
The quality of PrintPolymer signs truly sets the product apart from other techniques. Typical concerns of sign contractors, architects, and property owners when needing ADA signage is ensuring it will last for years. PrintPolymer produces the elements of wayfinding and room ID signage together as one product, so no pieces or paint would chip off the sign.
Photopolymer has been the preferred method of ADA signage creation by architects and signage professionals for years. While photopolymer still has digital capabilities in printing, the light curation process makes it susceptible to missing fine details that could be desired by a client. Time is wasted with physical labor needed to wash, cure, and apply paint to the signs, whereas PrintPolymer is ready for cutting and delivery minutes after it is printed.
Raster Braille printing is the most traditional measure used to create ADA signage. This method does not compare in terms of speed and durability with other forms of manufacturing. The beads used in raster braille are able to be tampered with, along with the other elements that are glued to the base substrate. While the creation of Raster Braille signs is cheap, production is slow with the need for manual labor in piecing the signs together. If you are looking to fulfill a project with a few hundred room IDs, this method could be painstakingly slow.
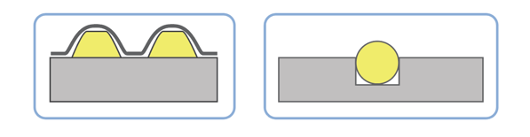
Photopolymer with paint on the left, Raster Braille on the right. Image from NovaPolymers.
Technique | Cost | Production Speed | Customization | Durability |
PrintPolymer | One single product results in cheaper cost, only material needed is ink and substrate | 6″ x 8″ (15cm x 20cm) MEN ADA/Braille sign prints in less than 1 min. 30 secs, ADA 14 sq ft/hr on same substrate, Textured detailing 32 sq ft/hr. Once printed, signs can be cut and shipped. | Virtually any design possible, photo-quality | Tamper resistant, Lasts 7-10 years |
Photopolymer | Expensive, multiple pieces (templates, chemicals) needed to complete one project | Requires more time/labor with washing and drying process | Designs can be replicated, but colors limited | Tamper resistant, prone to manual error, paint may chip off |
Raster Braille | 10-15% cheaper per sign than photopolymer, but need constant replacing for damaged parts | Manually creating all pieces of the sign results in slow process | Limited selection for designs and colors | Weak, very easily tampered, braille beads can come out of drilled holes. |
Thermoformed | Production process cheaper, but need of molds and acrylic powders | Manual labor of pressing signs together, waiting for heating/cooling process | Designs can be replicated, but colors limited | Tamper resistant, prone to manual error, paint may chip off |